Register Link for PAYESH SANAT KAVIR Courses
ثبت نام در دورههای پایش صنعت کویر
Training with testing AND Analysis
تقویم آموزشی دوره های داخلی
Payesh Sanat Kavir Course Calendar
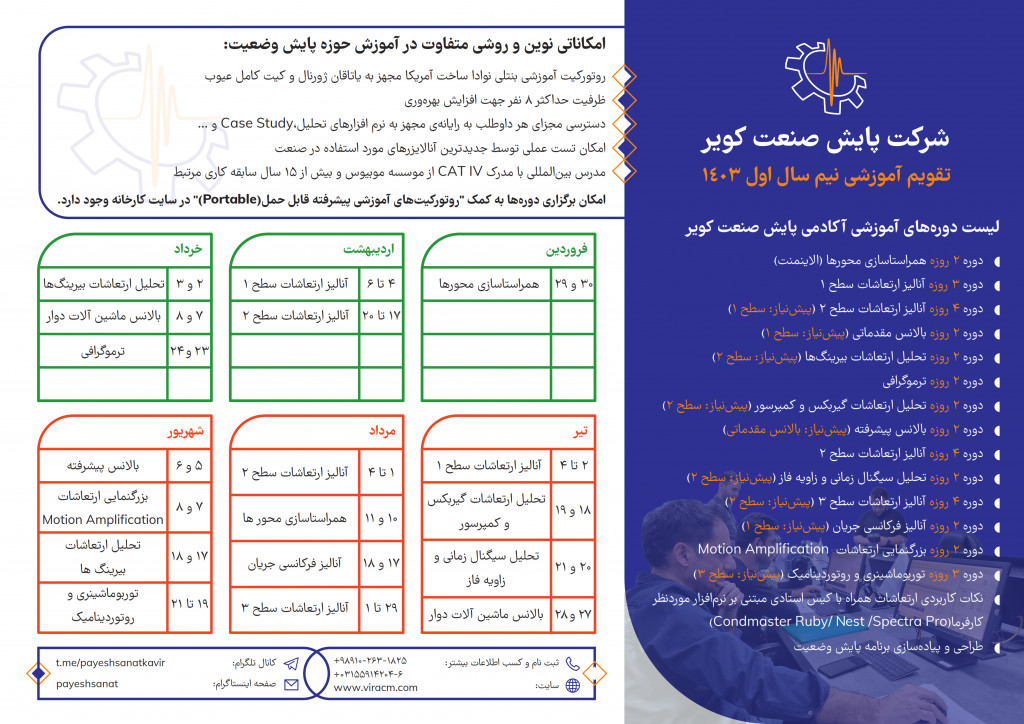
Register Link for PAYESH SANAT KAVIR Courses
ثبت نام در دورههای پایش صنعت کویر
Training with testing AND Analysis
تقویم آموزشی دوره های داخلی
Payesh Sanat Kavir Course Calendar
Rolling Bearings are vital components in various industries and ensure accurate and smooth rotation of equipment.
Various defects and failures can happen to them, which prevent their efficiency and proper functioning.
Bearing failure creates many parallel and simultaneous patterns. Full knowledge of these patterns helps us to diagnose their failure with sufficient confidence even without “having enough information about the bearing number”.
An example of vibration techniques for detecting bearing defects that we can use to correctly diagnose the failure and estimate its severity:
A- Frequency spectrum Symptom of Vibration velocity spectrum)
B-1 Vibration acceleration spectrum: Frequency spectrum Symptom
B-2 Vibration acceleration spectrum: Noise floor
C- Pattern of time signal Vibration acceleration
D- Frequency spectrum Symptom of acceleration envelope
E- Evaluation of the value or changes (trend) of the values of different parameters
Each parameter gives us a value that hopefully represents the health or failure of the bearing. Certainly, if this method (method E) is highly reliable, it will greatly reduce our work in reducing analyzes (methods A to D)
To use a parameter correctly, it is necessary to know exactly how it is calculated, because only in this case we will be able to have a correct understanding of its accuracy and the reason for its changes under different conditions.
In various industries, we have seen that the incorrect use of parameters has led to premature replacement of healthy bearings or even jamming of the bearing without warning.
For this reason, in the training course “BEARING DAMAGE VIBRATION ANALYSIS”, while testing several different failures, we examine the effect of failure severity and rotation speed on the values of different parameters.
We also examine the theoretical concepts related to these parameters and the conditions under which these parameters have errors.
Also, in order to increase accuracy, we will examine how to “simultaneously use” the “above techniques (A to E)” so that we can ensure the presence of failure and the severity of failure growth with sufficient confidence.
Today, different equipments offer different parameters according to their available signal processing and sensors:
In this brief article, we review some of these parameters:
BC- Skew- BCU -HDM- dBM- SFx-Spike Energy- Peak value-Crest Factor- Envelope Parameter
dBM parameter of the SPM Sock Pulse Method: Is calculated from the statistical analysis of the detected signals at very high frequencies.
HDM parameter: It is an improved method of dBM parameter.
BC parameter: It is the RMS value of acceleration signal with high-pass filter.
BCU parameter or Bearing Condition Unit: It is a parameter that expresses the condition of the high frequency vibration range.
The parameters extracted from the envelope signal: These parameters are depend on the demodulated acceleration signal in the considered frequency band. Considering that the signal is manipulated in the envelope process, the obtained units are not standard and different equipment use different units to express the value of the envelope signal. Such as: eu, Hdrp, gE, …
Kurt or Kutosis parameter: Kurtosis; the amount of transients in the vibration signal “tailedness” of the probability distribution of random variable.
Crest Factor parameter or sharpness index: It shows the ratio of the peak value to the RMS value. To diagnose bearing failure, this parameter is often checked in the acceleration unit.
RMS parameter: shows the RMS value of the signal. To detect bearing failure, this parameter is often checked in the acceleration unit.
Some of the out cases ostudy whose will be analyzed individually by candidates
IEC 60034-14:2018 RLV
Redline version
Rotating electrical machines – Part 14: Mechanical vibration of certain machines with shaft heights 56 mm and higher – Measurement, evaluation and limits of vibration severity
TC 2
Abstract
IEC 60034-14:2018 RLV contains both the official IEC International Standard and its Redline version. The Redline version is available in English only and provides you with a quick and easy way to compare all the changes between the official IEC Standard and its previous edition.
IEC 60034-14:2018 specifies the factory acceptance vibration test procedures and vibration limits for certain electrical machines under specified conditions, when uncoupled from any load or prime mover. It is applicable to DC and three-phase AC machines, with shaft heights 56 mm and higher and a rated output up to 50 MW, at operational speeds from 120 min–۱ up to and including 15 000 min–۱. This new edition includes the following significant technical changes with respect to the previous edition:
Improved explanation of the definition “free suspension”
Addition of an alternative method of rigid mount
Definition of an improved option for shaft key
۱۰۳۵-IEC60034-14-2018-Preview-en
The verification of the accuracy and repeatability of transducers and measurement electronic systems is called calibration. Vibration transducers are calibrated by subjecting them to a known motion and accurately measuring the electrical output. They are normally routinely calibrated at one-year intervals, and more often if they are subjected to damaging stresses.
Suggested Actions Based on Temperature Rise
This document has been prepared based on manufacturer instruction bulletins, NFPA, IEEE, NEMA and ANSI standards
Guideline VDI 3836 lays down criteria for the evaluation of vibrations in screw compressors and Roots blowers when measurements are taken at the non-rotating and rotating components of these machines in their place of installation. These criteria are also applicable to acceptance measurements of compressor stages carried out in the manufacturer’s test facilities.
As a basic rule, guideline VDI 3836 applies to rigidly or resiliently mounted compressors with outputs as shown in Table 1 of Section 4.1.2, when powered by an electric motor or a steam turbine. In the case of multiple-stage compressors of compact design the evaluation criteria should be applied to each of the stage air ends.
For less powerful machines, application of this guideline can be agreed on between the manufacturer and the customer.
Guideline VDI 3836 does not apply to compressors powered by internal combustion engines. The evaluation criteria presented in guideline VDI 3836 do not apply to the vibrations of the driving machines, which should be evaluated on the basis of the corresponding standards.
Guideline VDI 3836 applies to measurements made on the air ends itself at the measuring positions given in Section 2.3 and under the operating conditions explained in Section 2.6. In the case of measurements of non-rotating parts the evaluation variable is the root-mean-square value of the vibration velocity in two frequency ranges with different upper limits.
Frequency range A covers all major mechanical and flow-related vibration excitations. The additional frequency range B covers only those vibration components with single and doubled rotational frequency of the rotors which usually originate in imbalances. Assessments are given for both ranges in Section 4.
If, in the case of compressors with rotors running on sleeve bearings, the rotor vibrations relative to the bearings are measured, the characteristic variable will be the greatest value of the vibration amplitude (peak-to-peak value S(p-p)) of the vibration displacement.
The assessment criteria mentioned in Section 4 only apply to such vibrations as the compressor generates itself and not to vibrations which are transmitted to the compressor from the driving machine or from external sources. The assessment criteria mentioned in Section 4 are not suitable in the case of compressors for assessing the condition of built-in roller bearings, drive gears, or screw meshing. Information on measuring and assessing structure-borne sound of roller bearings may be found in guideline VDI 3832.
The machines forming the subject of this guideline are subdivided into four groups:
Group 1: Screw compressors with sleeve bearings and timing gears. Screw compressors for process gases normally belong to this group.
Group 2: Screw compressors with roller bearings or roller and sleeve bearings and timing gears. Oil-free air screw compressors will normally be classed with this group.
Group 3: Screw compressors without timing gears. Oil-flooded screw compressors will normally fall in this group.
Group 4: Roots blowers with roller bearings and timing gears